Modern manufacturers must overcome many challenges to remain competitive in an increasingly global market. Some of these challenges are new, such as understanding and implementing sophisticated automated technologies, while others are old news to manufacturers, like finding skilled workers and managing inventory. Either way, manufacturers of all sizes can benefit from a deeper appreciation of their biggest challenges. By implementing strategies to address the 18 challenges discussed in this article, manufacturers can improve efficiency, increase profitability and build long-term success.
What Are Manufacturing Challenges?
Manufacturing challenges can be any obstacle that hinders operations and impedes growth for manufacturing businesses. These challenges, such as regulatory compliance, supply chain disruptions and data security, directly affect many aspects of a manufacturing business, including production rates, productivity and profitability. Manufacturers cannot overcome these challenges without first understanding the ins and outs of their business. To do so, modern manufacturers can use new technology, including sophisticated business software and automation, to increase their visibility, gain a more detailed and accurate view of operations and identify vulnerabilities and opportunities for improvements. By understanding the unique issues facing the manufacturing sector and analyzing how operations are directly affected by these challenges, business leaders can devise and implement innovative solutions to create a more resilient operation.
Key Takeaways
- Manufacturers face both internal challenges, such as inefficient management and staffing issues, and external pressures, including shifting market trends, evolving customer preferences and supply chain disruptions.
- By understanding and proactively addressing these challenges, manufacturing professionals can implement new strategies to maintain their competitive advantage and increase profitability.
- Modern technology helps manufacturers mitigate the impact of these challenges and create a more flexible and resilient organization that is better equipped to overcome future obstacles.
Manufacturing Industry Challenges Explained
The manufacturing industry faces a barrage of constantly changing challenges. According to the National Association of Manufacturers’ Q3 2023 Manufacturers’ Outlook Survey, only 65% of manufacturing executives surveyed said they’re feeling positive about their company’s outlook — the lowest percentage in more than three years. Additionally, those surveyed said they expect costs to rise faster than growth. However, many manufacturers are beginning to feel better about the economy as a whole, with only 42% of respondents expecting a recession, down from 57% the prior quarter.
To better weather these conditions, manufacturers must take a close look at the challenges they face and strategically plan for the future. Many issues stem from external factors, such as technological advancements, shifting market trends and regulatory changes. But manufacturers also face internal challenges, including inefficiencies in inventory management, staffing shortages and low worker safety standards. By proactively monitoring and addressing these challenges, manufacturers can create a more effective operation and build long-term success. However, they must be sure to carefully plan and implement these new strategies deliberately. Rushing new technology or investments can strain resources and end up reducing efficiency, potentially resulting in additional challenges and frustrated staff.
18 Top Manufacturing Industry Challenges
Below are 18 of the biggest internal and external challenges facing manufacturers. Manufacturing professionals can study these challenges to help inform their strategies and build a more resilient and profitable business.
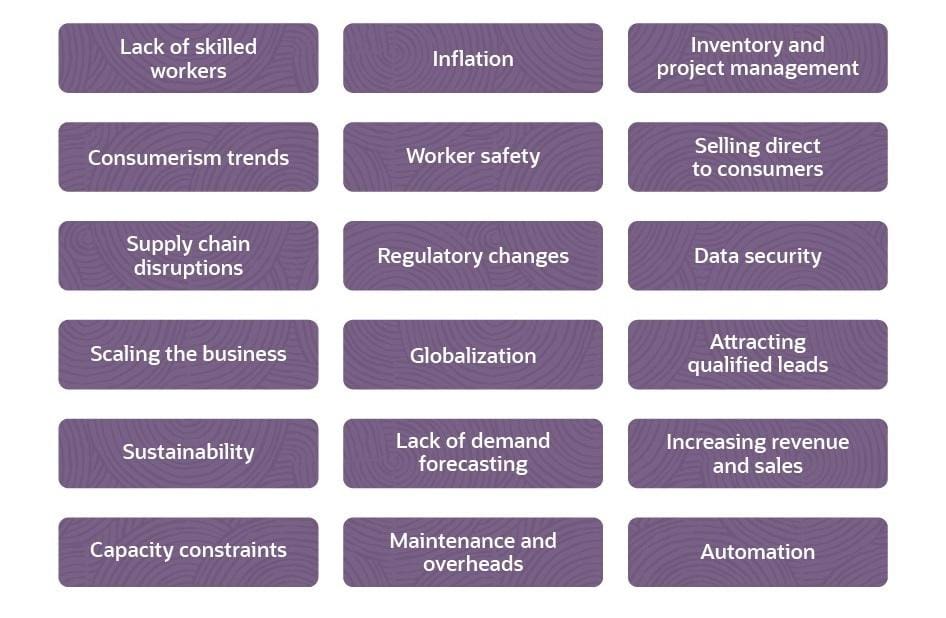
1. Lack of skilled workers: Many manufacturers face a significant shortage of skilled workers, with more than half (53%) of manufacturing executive respondents to Deloitte’s 2022 Manufacturing Supply Chain Study citing talent shortage as a top challenge. Talent shortage can be caused by several economic forces, including an aging workforce and a lack of tech-savvy workers. This scarcity has led to rising labor costs. In Q1 of 2022 alone, total hourly compensation in the manufacturing industry rose 6.2%, according to Deloitte. To address this challenge, many manufacturers track industry trends, such as wages and benefits packages, to ensure that they offer competitive employment options to retain workers. Manufacturers can also enhance their current workforce by investing in technology training programs. Additionally, many manufacturers partner with local community organizations and educational institutions to create creative recruiting strategies, such as internships and work programs, to bring in more skilled workers.
2. Inflation: During inflationary periods, prices rise across the economy, impacting just about every industry, including manufacturing. As costs rise, manufacturers seeking to maintain their margins face pressures to either raise their prices or reduce their costs. These costs include raw material procurement, freight and transportation and rising wages. Many manufacturers spend inflationary periods reassessing where to reduce costs, such as renegotiating supplier contracts or auditing their supply chains to find inefficient areas that can be improved without compromising quality and employee satisfaction. Additionally, if competitors’ prices are rising, manufacturers may be able to pass some of these higher costs on to customers without losing business.
3. Inventory and project management: Effective inventory management helps manufacturers find the balance between having enough stock on hand to meet customer demand and minimizing excess to reduce storage costs and clutter. To maintain that balance as customer demand evolves, project management involves detailed planning, coordination and execution of production processes to keep operations on schedule and on budget. However, many of these challenges are exacerbated by external pressures that are difficult to manage internally. These external pressures include demand fluctuations, supply chain disruptions and difficulties coordinating among the multiple parties involved in manufacturing projects. To more effectively track all these inventory variables, managers can leverage advanced inventory and project management systems, typically integrated within a larger enterprise resource planning (ERP) solution. These solutions use automation and centralized data to more accurately forecast demand and give managers real-time visibility into their operations, enabling them to make agile, data-driven decisions and quickly pivot operations when conditions change.
4. Consumerism trends: Keeping up with consumerism trends can be difficult, especially in the fast-paced ecommerce world, where products can go viral overnight. Many customers prioritize more than just price when shopping, considering factors such as ethical production processes, a personalized shopping experience and fast shipping options. However, without careful and deliberate planning, these offerings can lead to higher production costs and lower product quality. To satisfy modern customers without falling behind, manufacturers need to be more customer-adaptive, innovative and agile, often through a combination of market research, targeted product development and data-driven digital advertising — all with the ultimate goal of building reliable brand awareness that customers trust.
5. Worker safety: The nature of manufacturing work often involves heavy machinery, hazardous materials and strenuous physical labor, all of which pose safety risks to employees. Manufacturers must prioritize a safe working environment, not only as a moral obligation, but also to comply with regulations. Failure to comply with local worker protections and safety standards can lead to accidents, injuries and financial and legal liability. To ensure a safe work environment, manufacturers must implement regular safety training and properly allocate protective equipment. After safety protocols are established, managers must continuously monitor and update them to ensure that working conditions are up to current standards. However, maintaining these high safety standards is not without costs, and manufacturers must be prepared to invest in new equipment, continuous training and the latest technologies to ensure worker safety, including automation for high-risk jobs. When done correctly, prioritizing worker safety not only protects employees, but also contributes to increased productivity and morale, ultimately benefiting both staff and the business.
6. Selling direct to consumers: Online platforms have allowed manufacturers to bypass traditional retail channels and sell their products direct to consumers (D2C), causing a significant shift in manufacturing operations. By cutting out third parties, selling D2C can bring manufacturers increased profit margins and greater control over brand image, but it also presents unique challenges. Manufacturers that directly sell goods must operate their own ecommerce operation, including website management, digital marketing, returns and customer service. This also requires logistics management, including inventory control, order fulfillment and shipping. Many modern manufacturers rely on technology to overcome these challenges. For example, order fulfillment systems with scanners and automated data collection that tracks orders and monitors key performance indicators (KPIs), such as lead times and perfect order rates, help ensure that customers get what they ordered, when they expect it.
7. Supply chain disruptions: Many modern manufacturers rely on complex global supply chains, and disruptions present a significant hurdle for the industry. These disruptions stem from diverse causes, such as geopolitical conflicts and extreme weather events, and can slow shipments, reduce product quality, increase costs and lead to resource scarcity. Manufacturers can prepare for these complications by strengthening existing supplier relationships to gain preferential treatment; diversifying their supplier base; and leveraging digital tools for better visibility, including dashboards and KPI monitoring software. In fact, strengthening existing relationships and diversifying suppliers were the top two supply chain risk mitigation strategies listed in the Deloitte supply chain study, with 83% and 81% of executives emphasizing them, respectively. By anticipating these disruptions through data analytics and strategic planning, manufacturers can better weather supply chain complications, mitigate negative impacts when disruptions occur and stay ahead of the competition.
8. Regulatory changes: Navigating the ever-changing landscape of manufacturing regulations requires ongoing vigilance and updating. These regulatory changes impact many areas, including product safety, environmental impact and labor practices, and can significantly affect business operations. For example, a shift in carbon emission regulations might require manufacturers to invest in more efficient equipment to reduce emissions. If the manufacturer has facilities in different locations, each one may have different rules that must be followed. Noncompliance can lead to financial and legal consequences, as well as damage a company’s reputation. Therefore, manufacturers must stay current with regulatory updates through regular compliance audits, often by relying on external experts who closely follow changes in the industry and/or software to monitor compliance. By regularly updating their standards and protocols, manufacturers can stay ahead of upcoming regulatory changes to spread out the investment costs. These investments may come with additional benefits, such as potentially reducing costs and building a more efficient operation.
9. Data security: Modern manufacturers increasingly rely on technology and digitalization, leading to an increased emphasis on the secure collection and storage of vast amounts of sensitive data. Data breaches pose significant risks, including financial penalties and regulatory consequences. Additionally, manufacturers often suffer reputational damage after a data breach, which can hurt revenue when customers no longer feel that their personal and financial information is secure and take their business elsewhere. Businesses must regularly check and update their data security protocols, and many cloud-based business platforms will automatically update software and use artificial intelligence (AI) and machine learning to identify and react to the latest cybersecurity threats. However, data security measures include more than just encrypting information — though that is a major challenge on its own. Robust cybersecurity also requires regular employee training to proactively prepare staff for external threats, such as malware, ransomware and phishing attacks. Manufacturers should also have a recovery plan to minimize downtime and ensure business continuity if data breaches or shutdowns occur.
10. Scaling the business: Growing manufacturing businesses are faced with a tough challenge — timing. Scale too early, and manufacturers can face financial strain and operational challenges from dead stock and overstrained resources. Scale too late, and they risk missing profit opportunities and falling behind competitors that are seizing a larger market share. Technology can help manufacturing professionals get the timing right as they scale, with ERP solutions offering tools to effectively manage growth and create scaling strategies based on real-time data, not hunches. By leveraging these tools, manufacturers can develop a comprehensive strategic plan to align operations with overall business goals, market trends, competition and technological advancements. This helps manufacturers meet increasing demand, while minimizing the risks of bottlenecks and delays from pushing operations too quickly and exceeding production capacity.
11. Globalization: Globalization presents challenges for the manufacturing industry, but it also presents opportunities. On one hand, it increases competition, as manufacturers must compete with companies from around the globe. On the other hand, it can open new markets and allow for more diverse material sourcing from different parts of the world, potentially reducing costs and minimizing the risk of a single-source disruption leaving a manufacturer unable to produce goods. Overcoming these challenges and seizing these opportunities requires manufacturers to deftly navigate the complexities of international trade regulations, cultural differences, fluctuating exchange rates and more. To adapt to this global mindset, manufacturers can leverage technology, such as ERP systems, to manage these complex supply chain issues, automatically convert currency calculations, ensure compliance with international standards and effectively compete — and succeed — in the global market.
12. Attracting qualified leads: Manufacturers relying on traditional marketing strategies to attract qualified leads may be left behind as savvier competitors rise to the top of the highly competitive digital market. Modern marketing strategies often focus on building trust through relevant and targeted advertising and are crucial for generating leads. However, the personalized nature of these ads, tailored to each potential customer’s unique preferences and needs, can create management challenges for manufacturers. Some manufacturers benefit from partnering with marketing agencies with industrial expertise to better understand their target customer bases and how best to reach them. Additionally, manufacturers can use software with built-in sales dashboards to effectively leverage data to track marketing KPIs, such as conversion rates and cost per customer acquisition, to inform strategies and replicate successes.
13. Sustainability: Sustainability has become a major aspect of manufacturing, not just for its role in reducing costs and improving efficiency, but also to meet the demands of increasingly environmentally conscious consumers. However, achieving a sustainable manufacturing operation typically requires significant investment. Through collaboration among departments and with environmentally conscious consultants, manufacturers can effectively evaluate the potential costs and impacts of sustainability strategies, such as conserving energy and using environmentally friendly materials. This strategic approach can help ensure that manufacturing leaders are making sound investments to reduce their environmental footprint.
14. Lack of demand forecasting: Without reliable demand forecasting, manufacturers may experience losses due to overproduction or underproduction. Overproducing goods leaves manufacturers with shelves cluttered with dead stock, increasing carrying costs and slowing operations. Underproduction can lead to stockouts and frustrated customers. Both can result in reduced profits and customer dissatisfaction. To improve demand forecasting, manufacturers can leverage advanced technologies to collect and analyze detailed and accurate sales data to better align production schedules with market trends, customer behavior and other factors that influence demand. By doing so, managers can make more informed decisions to optimize production processes and better meet customer needs.
15. Increased revenue and sales: As a manufacturer’s revenue and sales, so, too, does the complexity of tracking and monitoring incoming orders. Managers must carefully monitor production to make sure that the higher order volume can be fulfilled and customer demand can be met on time and without sacrificing quality. Additionally, business leaders must track financial performance and cash flow to ensure that as sales increase, accounts receivable is keeping pace and effectively collecting payments from customers. Similarly, higher production volumes typically lead to higher costs, and financial teams must make sure to pay bills on time or risk harming relationships with suppliers and accruing additional penalties and fees. By carefully monitoring performance during growth periods, manufacturers can make sure that increased revenue and sales lead to higher profits and business growth without putting unnecessary strain on operations.
16. Capacity constraints: As manufacturers increase sales, they must also keep an eye on production capabilities. By overexerting processes, manufacturers can create bottlenecks, leading to missed deadlines, dissatisfied customers and lost business opportunities. Overcoming these limits on production, known as capacity constraints, requires a multifaceted approach that includes regularly evaluating business performance through order fulfillment KPIs, such as lead times and turnover rates. Businesses struggling against capacity constraints can identify bottlenecks by using a centralized ERP system to gain a holistic view of their supply chain. Manufacturers with a streamlined view of operations, including production, inventory and sales, can better understand their capabilities and gain insights into what improvements are needed to support larger order volumes — ultimately earning the business more revenue and higher profits.
17. Maintenance and overheads: For manufacturers, maintenance and overheads make up a large portion of costs and must be carefully managed to prevent wasted resources and frustrating slowdowns. Manufacturers require functioning and efficient equipment to meet production deadlines and customer demand. Regularly testing efficiency with performance-monitoring technology allows manufacturers to take a proactive approach to repairing, updating and replacing equipment. This often saves money in the long run with small, predictable repairs, rather than large overhauls when equipment unexpectedly breaks. Additionally, other overhead costs, particularly those associated with inventory and storage, can be reduced by adhering to data-driven demand forecasts to minimize overproduction and carrying costs.
18. Automation: Automation is more than just robots on the assembly line, though many companies greatly benefit from automating some of their direct manufacturing processes. Automation can be implemented throughout a manufacturer’s organization, including data collection and quality control. Manufacturers must use automation strategically, however, as the initial investment can be sizable. This investment requires both financial resources and time and labor to train staff to properly use these tools to increase productivity and benefit the business. But when implemented properly, automation can reduce labor costs and minimize many manual, error-prone tasks, such as counting inventory and tracking orders as they move through the supply chain with automated barcode scanners. With careful planning, manufacturing leaders can use automation to speed up production lines, streamline inventory management and create a more efficient company with lower costs and higher margins.
How Technology Can Help Solve Manufacturing Challenges
Technology is constantly changing how manufacturers operate. Manufacturers can benefit from recent technological advancements, including sophisticated ERP software systems designed to increase visibility. These systems collect far-reaching data and organize it into digestible financial reports and dashboards to help managers and decision-makers identify KPI trends and find areas for improvement. These systems also use automation and machine learning to help decision-makers better model scenarios and develop actionable strategies to improve operations, increase profitability and gain competitive advantages.
The interconnected nature of modern business systems allows manufacturers to implement other technology, such as the Industrial Internet of Things (IIoT) devices that collect and report real-time information. This up-to-date information gives managers and decision-makers detailed insights into potential bottlenecks, slowdowns and complications throughout the manufacturing process. This technology is especially important as supply chains become more complex and global because large, disjointed supply chains are more likely to experience disruptions and slowdowns. By proactively identifying weaknesses and vulnerabilities, manufacturers can plan contingencies to better address future challenges.
Get Better Visibility Into Your Manufacturing Supply Chain With NetSuite
Manufacturers need detailed strategies to stay competitive in the fast-paced modern market. But crafting those strategies requires real-time transparency into operations and performance, an especially challenging task as globalization continues and supply chains grow more complex. With NetSuite for Manufacturing, manufacturing professionals can control, coordinate and manage every aspect of their business from a centralized hub. NetSuite’s platform is built to address the unique challenges manufacturers face and provides a customizable and flexible business system to fit a company’s specific needs, both now and as they evolve.
With NetSuite’s ERP system, manufacturers can integrate sales, inventory, demand planning and more into a unified cloud-based platform for easy and secure access for all authorized parties — anywhere, anytime. From materials procurement to final delivery, NetSuite gives business leaders the tools they need to ensure that operations are running smoothly and delivering for customers. With NetSuite, decision-makers can be confident that they’re working with the most up to date and accurate information as they address today’s manufacturing challenges and prepare their companies to face tomorrow’s.
#1 Cloud ERP
for Manufacturing
Manufacturing Challenges FAQs
What are some challenges faced by a manufacturing company?
Manufacturers face many challenges, including rising costs, talent shortages and capacity constraints. Business leaders must plan and implement deliberate strategies to overcome these challenges and remain competitive, especially in the fast-paced world of direct-to-consumer ecommerce manufacturing.
Why is manufacturing so slow right now?
Manufacturing is especially sensitive to global supply chain slowdowns, including those resulting from trade disputes and wars. These slowdowns cause resource scarcity and bottlenecks in transportation. But by diversifying suppliers, monitoring supply chain pressures and implementing new technologies, manufacturers can overcome these challenges and build a more resilient manufacturing operation that is better prepared to serve its customers into the future.
What affects the manufacturing industry?
The manufacturing industry is affected by external pressures, such as regulatory changes, shifts in consumer demands and inflation. To maintain margins and build success, manufacturers can invest in more efficient equipment, technology and processes to streamline operations and reduce costs. They can also do market research to track competitors’ performance, employment offerings and prices to ensure that they remain competitive and don’t lose business or miss potential profit opportunities.