Benchmarking is critical to finding ways to make manufacturing operations run as efficiently and effectively as possible. We share how and what to benchmark in the manufacturing industry, best practices and examples to give you the competitive edge.
In this article:
- How to perform benchmarking in the manufacturing industry
- The types of benchmarking you can use to understand your business
- Examples of manufacturing benchmarks
- Benchmarking best practices
What Is Benchmarking in Manufacturing?
In manufacturing, managers use benchmarking to compare their business to other industry examples. Benchmarking in manufacturing can also find gaps in service delivery, measure and track improvements, and help a business succeed.
Key Takeaways
- Use benchmarking in manufacturing to look for improvements and become an industry leader.
- Perform benchmarking by following a phased approach of planning, analyzing, communicating, installing and remeasuring.
- There are five types of benchmarks in the manufacturing industry. Choose the metrics you need based on the company’s goals and desired market position.
What Is the Importance of Benchmarking in Manufacturing?
In manufacturing, benchmarking is an essential tool for improvement. Benchmarking looks at company and staff metrics across the industry. By comparing outcomes, the practice finds company gaps and weaknesses to address and change.
What Are the Benefits of Manufacturing Benchmarking?
Benchmarking benefits a business by ensuring it is competitive in its industry. The practice sets a precedent for staff to live up to or exceed. It also helps companies figure out when a product or process is underperforming and why.
Aside from distinct areas of improvement, benchmarking creates a mindset of continuous improvement. Market leaders exceed industry benchmarks.
Types of Benchmarking Used in the Manufacturing Industry
There are five types of benchmarks for the manufacturing industry. These types are internal, competitive, performance, functional and generic. Each class is a different level or aspect of the business and targets improvements with the right benchmark manufacturing KPIs.
-
Internal Benchmarking
Use internal benchmarking to compare different units, shifts, or divisions within your company to each other. Internal benchmarking can show if your company has unequal policies or circumstances that enable some areas to outperform others. One example of internal benchmarking in manufacturing is looking at production outcomes such as the number of units produced across different shifts.
-
Competitive Benchmarking
Use competitive benchmarking to compare your business to others like yours within your industry and those you consider peers. Competitive benchmarking shows your position in the marketplace overall. Examples of competitive benchmarking include metrics like market share or projected growth.
-
Performance Benchmarking
Use performance benchmarking internally or in comparison to other companies. This type measures product creation and getting those products into the hands of consumers. Examples of performance benchmarking in manufacturing are product creation, machine output and total manufacturing costs.
-
Functional Benchmarking
Use functional benchmarking when looking solely at the work function. You do not need to limit your comparisons to your industry or within your company. Regardless of the company or industry, these measures look at generic work processes or outcomes. For example, use functional benchmarking in manufacturing to measure inventory control or picking procedures.
-
Generic Benchmarking
Use generic benchmarking when comparing the work processes or conceptual outcomes between companies. These benchmarks are usually high-level and incorporate marketplace standards, not necessarily linked to a specific industry. For example, in manufacturing, generic benchmarks could be becoming more culturally competent in hiring or making your company more environmentally sustainable.
How to Benchmark in Manufacturing
In manufacturing, perform the benchmarking process in a phased approach. The steps are plan, analyze, communicate, install and remeasure. This method gives you a data-driven approach to continuous improvement.
-
Start benchmarking by planning.
Develop a plan of what and whom you want to benchmark based on known issues in your company and what your research reveals about your competitors. Bring your company’s subject matter experts in to discuss their process and performance concerns.
-
Analyze the metrics you measure.
Ask questions about why these measures look the way they do. For example, if you have an internal benchmark that shows different outputs between shifts, ask about the differences between those shifts. Determine why the metrics came out the way they did and set realistic goals for improvement based on the outcomes and explanations.
-
Communicate to your organization any new plans and get buy-in.
For example, staff needs to understand why you may be changing things to be on board with the new goals and new explanations.
-
Install the action plans and monitor how they are progressing.
Is there enough staff acceptance? Is there a better way to do things? Remeasure when enough time has passed to see a change in the data.
What to Benchmark in Manufacturing
In manufacturing, there are some key measures to benchmark. These metrics are the best ones to check your manufacturing performance. You should be looking at manufacturing cost, plant shipment values, machine downtimes and cycle times.
Keeping an eye on these measures and how they line up within your industry will help you find efficiencies in production schedules, workflows and machine maintenance. Overall, these are the critical ones to benchmark for continuous improvement and apply to regular and contract manufacturers.
Benchmark Manufacturing Costs
Manufacturing cost benchmarking should include KPIs for purchasing and production. Compare the data to your competition and market forces to improve efficiency. Manufacturing cost KPIs to benchmark include:
Total Cost to Manufacture
This measurement adds all reasonable expenses, such as the costs of labor and overhead. This metric varies by product but weighs heavily in end-consumer pricing.
Cost of Goods Sold (COGS) as Percentage of Revenue
This metric is the direct cost of producing the products your business sold. Generally, companies do not want to exceed 65% of their income in this metric.
Labor Costs as Percentage of Cost of Goods Sold
All associated labor costs go into this metric, including wages, benefits, salaries and training. Most companies should not exceed 20% to 35% of their labor cost for their gross sales.
Material Costs as a Percentage of Costs of Goods Sold
This metric is the combined expense of the raw materials compared to the COGS. Materials are typically about 50% to 75% of COGS.
Yield
The yield is the number of goods produced during the manufacturing process for a specified amount of time and output of specific raw materials and scrap. This measure shows production performance and whether your process changes improve efficiency.
Yield does not account for capacity, downtime or schedule challenges and can be wildly different between companies in the same industry and between products.
Benchmarking Manufacturing Productivity
Productivity metrics look at inputs such as labor and material and how adjusting them changes outputs. The following is a list of manufacturing productivity KPIs to benchmark.
Operator Loading
Use operator loading KPIs to measure the process control system in manufacturing. The control loops per operator review the number of times the control system process can run. The I/O per operator measures the input and output run per operator.
These figures consider the complexity of the system and the level of automation and vary widely across industries. Measure these to learn about the success of your improvements in coding and process.
Changeover Time
Changeover time is how long it takes to convert a line or machine from the good part of one run to the good part of another run. This time is entirely based on the product or machinery, and companies can optimize this timing with experience.
For example, change over time in automotive can take weeks, while some product changeover times can be minutes.
Capacity Utilization
Capacity utilization compares potential and actual output. This productivity metric should ideally be at 100%, and anything less indicates that production can increase without increasing overhead costs.
Order Cycle Time
This measurement is the average time it takes to fulfill an order from the time it was placed but not including the actual shipping time. This helps to measure the efficiency of your operations.
Schedule Attainment
Production schedule attainment can deliver the number of units promised in a production plan. This measurement incorporates a company’s ability to meet cycle times and maintain its equipment. This metric does not include defective products.
Primary Product Manufacturing Cycle Time in Hours
This measure is the manufacturing time for the company’s main product(s) from beginning to end. The benchmark depends specifically on the product but may be compared across different companies for that exact product.
Energy Management
Manufacturing plants have a metric to meet, called the ENERGY STAR score, from the U.S. Environmental Protection Agency (EPA). This metric measures them against other manufacturers (and themselves) to the percent energy managed or the amount of energy they expend.
The score also considers throughput, the energy that goes in and out of the facility. The EPA recognizes companies for achievement in these metrics.
Benchmarks for Manufacturing Equipment
Asset managers rely on manufacturing equipment benchmarking. The measurements speak to maintenance, cost, repairs and replacements. Equipment metrics affect cycle times and downtimes. The following is a list of benchmark KPIs for equipment KPIs.
Overall Equipment Effectiveness (OEE)
This metric is the most critical equipment KPI. The goal is always 100% OEE, as it is the percent of the time a machine is manufacturing good parts. This measure is based on availability, performance, and quality.
A 100% score means perfect production, with no downtime, good parts and a quick run.
Age of Plant
Also known as plant asset useful life or equipment age, the age of plant is the age of long-term assets, as noted on the accumulated depreciation divided by the annual depreciation expense.
This standard can be anywhere from 3-20 years for machinery and equipment, and for property, it can be 10-50 years.
Unplanned Machine Downtime
This measurement is the disruption time of a machine during production with unplanned downtime. Top performers have about 3% unexpected disruption time and bottom performers have about 6% disruption time.
The metric does not include scheduled downtime or unscheduled use time. This benchmark is less a measure of success and more a measure of prevention.
Return on Fixed Assets (ROFA)
This metric details how much a company makes in return for its long-term investments, such as equipment and property. Companies use these assets to generate revenue. To benchmark this metric, track the trend over time. You want it to be improving.
Asset Availability
Asset availability tracks how much downtime a piece of equipment has compared to its operating time. Expressed as a percent, this is a part of the OEE metric. The goal is 100%.
Planned Maintenance Percentage (PMP)
This metric is the amount of time needed and used for planned maintenance tasks based on the number of hours for the period. PMP should be better than 85%. Make improvements to this metric by improving adherence to a schedule.
Manufacturing Inventory Turnover Benchmarks
Inventory turnover ratio (ITR) metrics are the rate that companies make and sell goods. These measurements can be leading indicators of backorders or extra costs in procurement. You’ll want to benchmark the following inventory turnover KPIs.
Raw Material Inventory Days of Supply
This metric is the value of the raw materials inventory by the weight of transfers in the period. Optimizing this value means getting rid of waste.
Like other ITR measures, a good measurement is between five and 10, meaning that your company sells and replenishes stock every one to two months.
Finished Goods Inventory Days of Supply
This metric is akin to the raw material inventory days of supply but is for the finished goods. This rate is the number of days before the company sells all finished goods.
A high value means that the company’s inventory carrying strategy is lacking. A low value is also sub-optimal, as it implies that stockouts are likely.
Inventory Turnover
This basic formula compares the COGS and the average inventory level, irrespective of the type of material, over a year. Most experts put this benchmark as optimal between 1.0 and 2.0 for the year.
Learn more about inventory turnover, including calculations, rates and analyses. You can find more inventory management KPIs and metrics in our guide.
Fill Rate
Fill rate measures the percent of orders satisfied by the products currently in stock. A higher fill rate is preferable. Average companies keep their fill rates at 85% to 95%, while high-performing companies exceed 97%.
Benchmarks for Manufacturing Personnel
Personnel metrics in manufacturing are human measures. People are one of the costliest resources in any company. Manufacturing personnel may be more challenging to keep. These personnel KPIs should be on your list to benchmark.
Support Personnel Loading
This metric includes the total support personnel, the total process control personnel and the total system personnel. These are direct labor costs and helps add to the COGS.
Turnover Rate for Manufacturing Personnel
The turnover rate for manufacturing personnel is the ratio of how many personnel start, get trained and then voluntarily quit. This measure is high in manufacturing, with average rates of over 20%. In other industries, 10% is more the norm.
Providing better training and working conditions are ways to make improvements in turnover rate.
Manufacturing Financial Ratios Benchmarks
Benchmarking financial ratios for manufacturing shows whether a business is a decent long-term investment. These metrics show a company’s profitability and check the efficiency of the manufacturing process. Use the following list of financial ratios as benchmarks.
Value of Plant Shipments per Employee
This financial metric is also a performance metric of employees. This measurement shows employee engagement in the number of products they are personally responsible for shipping.
High-performing companies have this measure at around $450K per employee, while low-performing companies have it at about $200K less. Improve this metric by increasing employee engagement by creating space to listen to their ideas.
Revenue Growth
This metric is the month-by-month increase in revenue, showing either increase or decrease. The benchmarks for a manufacturing company depend on your company’s goals. These goals could be related to lifecycle, industry or change in the process.
Total IT Spend as Percentage of Revenue
IT is essential across all industries. Manufacturing has comparably low spending in IT next to other sectors. This spend is mainly on back-office products. Those that spend more do so on ERP-type programs that help track their metrics.
The average IT spend per revenue manufacturing firm is about 1.95%, according to Deloitte.
Example of Manufacturing Benchmarking
Every industry has its benchmarking examples and best practices. Examples of manufacturing metrics to benchmark include those that look at costs, equipment maintenance, the productivity of the warehouse and the personnel and finance.
Benchmarked metrics in the manufacturing space look at the functions specific to the warehouse, such as inventory turnover and process success measures. To find external manufacturing benchmarks, you’ll need to work with a company specializing in research and presentation of industry benchmarking. These organizations use a particular framework to present the benchmarks. You can use the following framework with four distinct levels:
- Foundational: This level is when a business is just getting into the metric’s space. They are new to the industry or the product line. Companies at the foundational level should be looking to make quick, aspirational improvements.
- Competitive: This level is when a business is doing well enough to compete but is still looking to make strides. Companies at the competitive level should focus on improving performance.
- Best in Class: This level is for businesses that lead in their industry. Their position may be due to a strict focus on that space. This level means they must start to optimize their functions to get to the next level.
- Transformative: At this level, a business has reached its optimum performance level and are genuine standouts in its industry. Other companies look to them for inspiration. At this level, invest in maintaining an organization’s advantages.
Example of Manufacturing Benchmark for Inventory Turnover
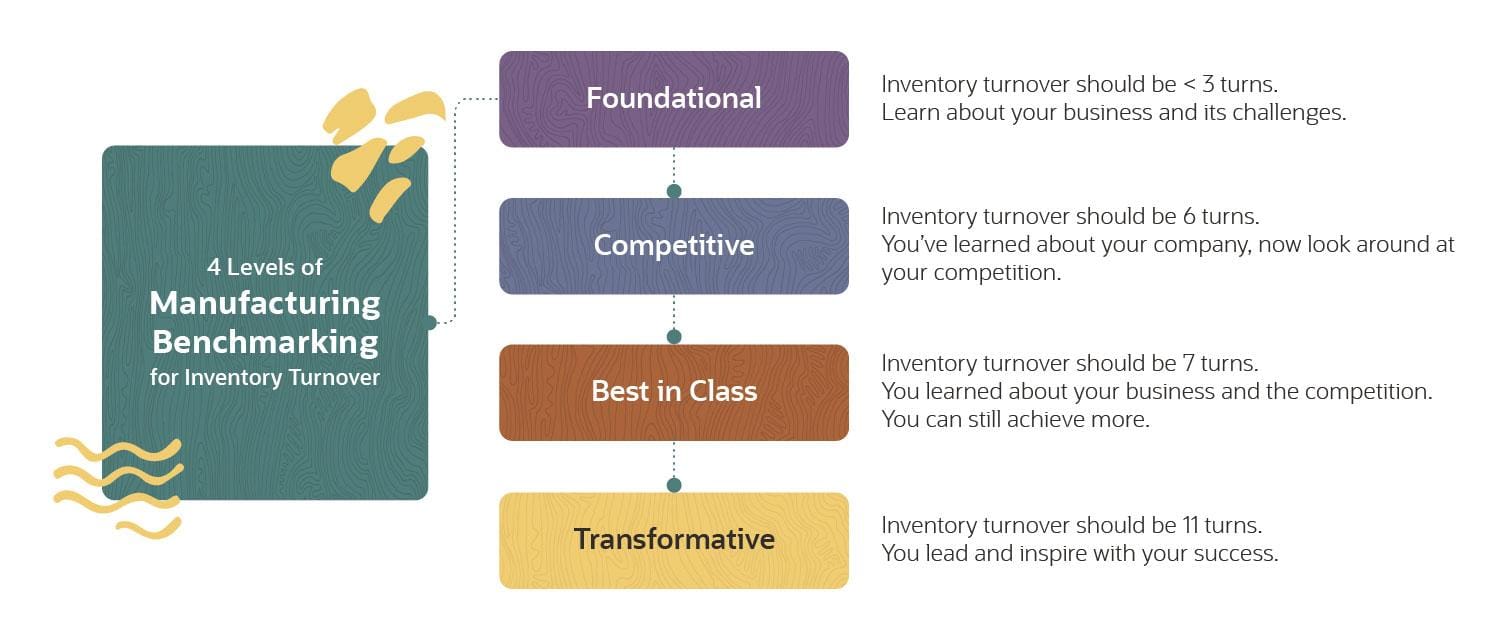
Examples of Manufacturing Industry Benchmarks
Metrics for manufacturing consider the various requirements for producing new products. The goal of these measures is to develop efficiencies in the supply chain, warehouse and logistics.
Look at measures such as order cycle times, fill rates, inventory turnover ratios, customer service responsiveness, total IT spend as a percentage of revenue, time to close books, revenue growth, ecommerce growth and days sales outstanding.
Read our guide to supply chain metrics and KPIs to see how those metrics can affect manufacturing benchmarks.
Best Practices in Benchmarking for Manufacturing
To get to superior performance, turn to best practices in benchmarking. Benchmark across all types: internal, competitive, functional, and generic. Use a phased approach, and these other best practices, including:
- Get a commitment from management to support benchmarking.
- Be willing to develop changes based on benchmarking process findings.
- Share information with partners.
- Maintain a continuous improvement culture. Our article, “Manufacturing Trifecta: Tariffs, Talent, Target Market Weakness,” has tips for making these changes in your business.
- Consider acquiring ERP software that tracks and reports your metrics regularly.
#1 Cloud ERP
Software
Software to Track And Report Your Benchmarking
Make your manufacturing benchmarking more efficient by using an integrated cloud ERP solution. NetSuite streamlines your data acquisition and reporting, collects valuable information from all your plants, and stores them in a central location. You can track and report while making improvements.
Look for a system that offers you multiple options to deploy your software. NetSuite provides an award-winning, centralized data solution so manufacturers can quickly access the data needed for benchmarking from the shop floor to the top floor. NetSuite’s customizable dashboards make internal benchmarking easy.